Singapore’s manufacturing workers are ageing. Here’s how to help them
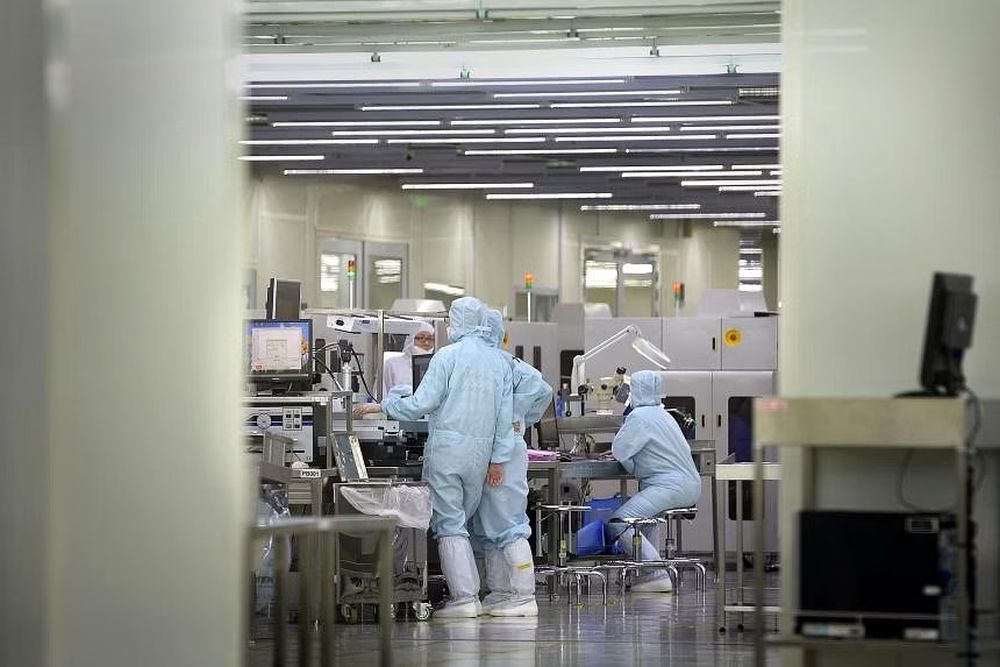
Published on
17 May 2024
Published by
The Straits Times
The sector is largely staffed with mature workers. Simple initiatives can ensure that they don’t get left behind.
Patrick Tay
Some may call this an opportunity and others may see it as a risk, but here is an important point to ponder: The average age of a manufacturing worker in Singapore is 50.
This is a risk because it highlights that the manufacturing sector is an ageing one. Yet, there is an opportunity to tap this huge pool of experience and human capital and make it even more effective through technology and support at the workplace.
The labour movement is invested in the sustenance of the manufacturing sector, which has consistently created good jobs for Singaporeans. Manufacturing is the bedrock of Singapore’s economy, contributing to a fifth of the nation’s gross domestic product. But as an export-oriented sector, it is vulnerable to external volatility. It shows more fluctuations than other sectors and has recurring patterns of downturns followed by recoveries.
What this means is that workers who have remained in the manufacturing sector across these ups and downs are resilient individuals who have secured a substantial stock of skills and experience.
These workers would have also made sacrifices for the sustenance of the local manufacturing sector.
In 1985, for example, Singapore experienced its first recession. Annual wages for a manufacturing worker fell from $16,073 that year to $15,193 in 1987. Employer Central Provident Fund contributions were cut by 15 per cent and a two-year wage restraint was introduced to keep the sector afloat.
These sacrifices did not go to waste – Singapore remained competitive and the manufacturing sector even benefited from the boom in personal computing in the following years.
That technological focus has accelerated in recent years, but are we at risk of leaving our most faithful workers behind? How might we continue to ensure that we do right by them, and that they are not alienated as a result of technological disruptions? How might we maximise the value of all their accumulated experience to further reinforce the manufacturing sector in years to come?
Studies have been undertaken to help these workers. In October 2023, the United Workers of Electronics & Electrical Industries launched the Jobs Uplifting Through Skills & Training programme. The focus was on the training needs of local operators and technicians – the majority of whom are mature workers, aged between 41 and 60.
Another project which involved NTUC Strategy looked at the future of manufacturing and examined the opportunities, tensions and risks that confront the sector today.
To help the mature workers in the sector, we need to develop the right infrastructure and also institutionalise knowledge transfer.
Getting the infrastructure right
As the workforce ages, there is a need to redesign our workspaces in order to accommodate different ages and physical abilities. What we call “factories-for-all-ages” would enable a multi-generational workforce to thrive.
Imagine a manufacturing plant fitted with ergonomic aid devices, such as back or knee supports. Or collaborative robots (cobots), specifically designed to perform routine or physically demanding tasks with remarkable precision. These robots can take over repetitive and strenuous duties. This will not only reduce the risk of worker injuries but also free up human workers to focus on more complex and value-added responsibilities.
We observed one such example at Positronic, where workers had to manually insert pins – a task that required enormous hand-eye coordination. It was also physically strenuous, especially when performed over an extended period. The company solved the issue by acquiring an automated contact-pin insert and seating machine with support from the Company Training Committee Grant. This freed up the operators, who are mainly mature local workers, to focus on value-added tasks like quality control, allowing for increased efficiency and productivity in the company.
Ergonomics and automation will empower workers to continue working into their later years, if they so choose.
Learning new tricks
Older workers have expertise and experience. Younger workers are more digitally savvy. We need to facilitate the transfer of knowledge between older and younger workers so that both groups gain and the sector benefits.
As older workers retire, we risk losing invaluable expertise. But we also risk leaving older workers behind if they are not equipped with knowledge and know-how related to the digital aspects of work, which come naturally to younger workers who acquired their technical skills in a digitalised setting.
Some companies are trying to address this by helping their mature workers navigate an increasingly digitalised world and workplace. For example, when Thales DIS obtained automated mobile robots to transport batches of hard-disk drives to and from stations in the production area, it freed up its operators to upskill through learning basic programming to operate the robots.
Similarly, Utac acquired virtual reality (VR) goggles to support training for its mature workers. The goggles were intended to acquaint its mature workers with VR technology to prepare them for the company’s eventual use of augmented reality goggles for live feedback. They were also intended as a safe platform for mature workers to gain confidence and minimise mistakes in machine handling.
Such initiatives are the first steps towards facilitating the transfer of knowledge between senior and younger workers. By providing learning opportunities and a supportive learning environment that ultimately champions human capital across all age groups, we can collectively work towards ensuring our workforce remains relevant without compromising on the evolving needs of companies.
Multi-directional mentorships, for example, recognise that learning and growth flow in multiple directions. It’s not just about an older employee mentoring a junior one – it’s also about creating a dynamic exchange of insights and skills across all levels. Imagine a seasoned worker sharing his wealth of experience with a fresh recruit, while the younger employee introduces novel ideas and technological know-how. This collaborative mentorship model enriches the entire workforce, improving domain-digital literacy for all workers in the workplace.
Inclusive, multi-generational workplaces send a powerful message: Everyone has a shared future. Workers of all ages can learn from one another. And everyone can work together in factories-for-all-ages. It helps the workers, the companies and the nation grow together. It also ensures that no one is left behind in an ageing world.
- Patrick Tay is executive secretary of the United Workers of Electronics & Electrical Industries and assistant secretary-general of the National Trades Union Congress.
Source: The Straits Times © SPH Media Limited. Reproduced with permission.
ALL views, content, information and/or materials expressed / presented by any third party apart from Council For Third Age, belong strictly to such third party. Any such third party views, content, information and/or materials provided herein are for convenience and/or general information purposes only. Council For Third Age shall not be responsible nor liable for any injury, loss or damage whatsoever arising directly or indirectly howsoever in connection with or as a result of any person accessing or acting on any such views, content, information and/or materials. Such third party views, content, information and/or materials do not imply and shall not be construed as a representation, warranty, endorsement and/or verification by Council For Third Age in respect of such views, content, information and/or materials.